As an important non-metallic mineral resource, pyrophyllite plays an indispensable role in traditional fields such as ceramics, refractory materials, chemicals, and construction, as well as emerging high-end fields such as electronics and aerospace. In the ceramic industry, pyrophyllite has significantly improved the quality and market competitiveness of ceramic products with its excellent plasticity and stable chemical properties. The market price of high-end ceramic tableware is therefore 20%-30% higher than that of ordinary products. In the field of refractory materials, the high refractoriness and low expansion of pyrophyllite extend the service life of high-temperature kilns and reduce maintenance costs.
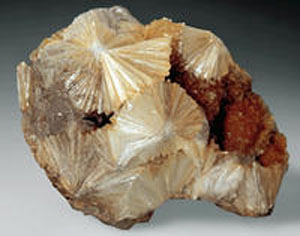
From the perspective of the scale of the Pyrophyllite Ore Market, the global pyrophyllite market has grown steadily, with an average annual growth rate of 8%. Asia is the largest consumer market, accounting for more than 65% of the global total consumption. The multi-field application and emerging demand of pyrophyllite are driving its continued market expansion, and its potential in high-end manufacturing and green energy will be further released in the future.
Innovative equipment improves crushing efficiency
The physical properties of pyrophyllite determine the equipment that needs to be adapted for its crushing. At present, jaw, hammer and roller crushers are commonly used pyrophyllite crushing equipment, each with its own advantages.

The jaw crusher is the preferred choice for coarse crushing, suitable for materials with a compressive strength of less than 320 MPa, and is widely used in metallurgy, construction and other industries. The deep cavity design improves the feed and output, and the large-sized and wear-resistant eccentric shaft bearings, combined with good sealing, extend the bearing life by 1-2 times. Advanced technology and design make the equipment simple in structure and stable in operation, achieving environmental protection and energy saving, high-intensity crushing reduces dust pollution, and reduces user costs by more than 15%.

The hammer crusher performs well in processing medium-hardness and brittle materials in mining, cement and other industries. The output particle size can be adjusted within 35mm as needed, with high production capacity. It has a compact structure, is small and light, and is easy to maintain. Good sealing solves the problems of dust and ash leakage. Important parts are made of new materials to enhance wear resistance and pressure resistance, reduce wear and extend service life, which can save users about 30% of maintenance costs each year and reduce costs.

Roller crushers are widely used in pyrophyllite crushing, metallurgy, building materials and other industries. The crushed products are mostly cubic, with less than 5% of needle-like materials and uniform particle size. Strong crushing force, stable operation, low noise, and environmental protection advantages. Using international advanced materials, the equipment has a long wear cycle, which extends the life of the machine body and brings considerable benefits to users.
Grinding process: advanced technology creates high-quality powder
Grinding is a key link in pyrophyllite processing, which directly affects the quality and application performance of the final product. Traditional pyrophyllite grinding processes mostly use Raymond mills, but due to the high hardness of pyrophyllite and the requirement for the fineness of pyrophyllite micropowder to reach 325 mesh or even higher in some application fields, Raymond mills expose the shortcomings of low output and high wear during processing.
To solve this problem, Cronus introduced advanced grinding technology and equipment, such as vertical mills. As a technological pioneer in the field of powder processing, Shanghai Cronus's vertical mills are specially designed for the grinding needs of high-hardness materials such as pyrophyllite. Cronus has been deeply involved in the field of powder equipment manufacturing for many years. With its deep technical accumulation and rich practical experience, it has launched a series of vertical mill products with excellent performance.
Parameter comparison table
Model | Output (t/h) | Motor Power (kW) | Weight (t) |
---|---|---|---|
CR1300 | 20-24 | 200 | 56 |
CR1500 | 25-34 | 280 | 68 |
CR1700 | 38-48 | 400 | 88 |
CR2000 | 65-80 | 500 | 115 |
Take the vertical mill of Shanghai Cronus as an example
Low construction cost: Compared with the ball mill system, the vertical mill occupies 50% less space and the construction cost is reduced by about 70%; because it integrates crushing, drying, grinding, and grading and conveying, the system is simple and can be arranged outdoors, with low investment and construction costs.
Low operating cost: high grinding efficiency and low power consumption, which reduces power consumption by 40-50% compared with the ball mill; the grinding roller and liner are made of high-chromium wear-resistant material, with less wear and long service life, reducing operating costs; it can be equipped with an external circulation device to further reduce power consumption;
Reliable operation: equipped with an automatic control device, which can realize remote control and simple operation; equipped with a limit device to prevent the grinding roller from contacting the liner, which can effectively protect the equipment;

Convenient maintenance: by inspecting the roller assembly outside the oil cylinder, the grinding roller and liner can be repaired and maintained better and faster;
Environmentally friendly and clean: low vibration, low noise, the system is in negative pressure operation, and there is no dust spillage;
Excellent quality: the material stays in the mill for a short time, which is easy to detect and control the powder degree and chemical composition of the product.
Selection suggestions
Small-scale production: Choose CR1300 or CR1500, suitable for users with low production requirements and limited space.
Medium-scale production: Choose CR1700 or CR2000, suitable for medium-scale production requirements, taking into account efficiency and cost.
Large-scale production: Choose CR2200 or CR2500, suitable for high-volume requirements, meeting industrial-grade production requirements.
Extra-large-scale production: Choose CR2800 or CR3400, suitable for extra-large projects, ensuring efficient and stable operation.
The Cronus vertical mill series can provide efficient and stable solutions.
If you still have questions or need more detailed model recommendations, please provide more specific information and we will provide you with more accurate suggestions. Choose Cronus vertical mill to help your production run efficiently!