Cronus Unveils Cutting-Edge Calcium Hydroxide Grinding System in Xinjiang, Showcasing Calcium Hydroxide Grinding Mill Raymond Mill Expertise
Xinjiang, China – Cronus, a globally recognized leader in Raymond mill manufacturing and mineral processing solutions, has commenced the installation of its specialized calcium hydroxide grinding system in Xinjiang, marking another milestone in its mission to deliver advanced, research-driven milling technologies to industrial clients. The project underscores Cronus’ unwavering commitment to innovation, its deep understanding of the calcium hydroxide industry, and its ability to tailor Raymond mills for niche applications.
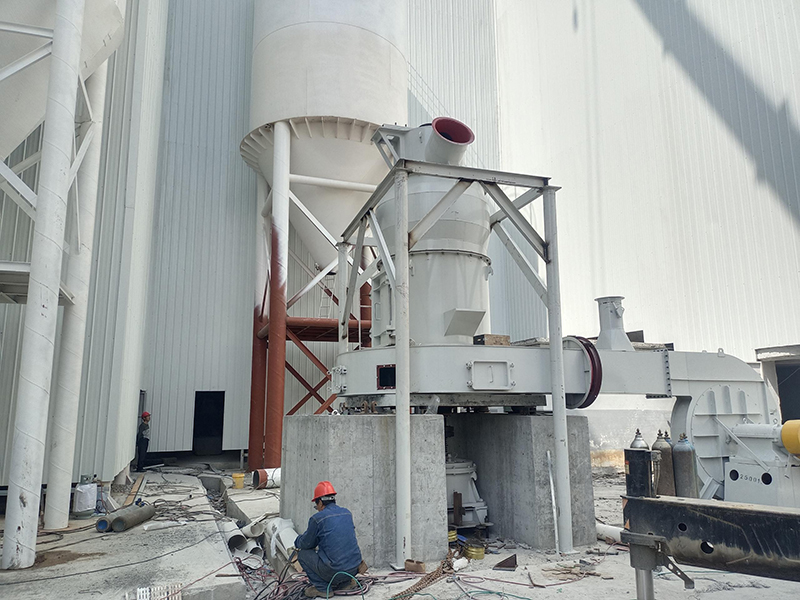
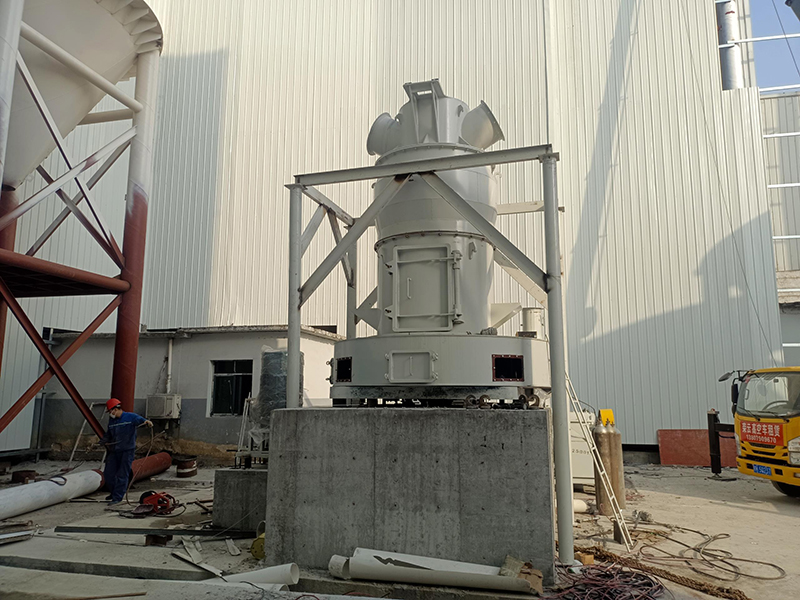
Cronus: A Legacy of Technological Excellence of Calcium Hydroxide Grinding Mill
For over two decades, Cronus has been at the forefront of Raymond mill engineering, serving industries ranging from mining and metallurgy to chemicals and construction. The company’s reputation rests on its relentless investment in R&D, with 15% of annual revenue dedicated to advancing grinding technologies. Its in-house team of 50+ engineers collaborates with universities and industry partners to address evolving challenges in mineral processing.
Recent breakthroughs include proprietary grinding ring designs, AI-driven particle size control systems, and energy-efficient airflow optimization—innovations that have earned Cronus 12 patents in the past five years. "Our philosophy is simple: every mill must solve a problem," said Dr. Li Wei, Cronus’ Chief Technology Officer. "For calcium hydroxide producers, that means tackling humidity sensitivity, dust control, and ultra-fine grinding efficiency."
Tailored Solutions for Calcium Hydroxide Challenges
The Xinjiang installation highlights Cronus’ ability to customize Raymond mills for calcium hydroxide (hydrated lime), a material critical to water treatment, flue gas desulfurization, and construction. Traditional mills often struggle with its sticky, moisture-laden properties, leading to clogging and inconsistent output.
Cronus’ engineers redesigned the grinding chamber with three key upgrades:
- Anti-Adhesion Coating: A nano-ceramic layer on rollers and rings prevents material buildup, ensuring smooth operation even at 8% moisture content.
- Multi-Stage Separation: A dynamic classifier with adjustable rotor speeds achieves 98% precision in producing 325–2500 mesh powder, meeting strict industrial specifications.
- Closed-Loop Dust Management: Integrated pulse jet filters and negative pressure systems reduce ambient dust to <10 mg/m³, exceeding China’s GB 16297-1996 emission standards.
The system’s 6-8.5 ton/hour throughput (30% higher than conventional models) and 15% lower energy consumption have already attracted attention from chemical plants across Asia. "We tested six mills before choosing Cronus," noted Mr. Zhang, the Xinjiang plant’s project manager. "Their engineers spent three months simulating our raw material conditions. The result? Zero blockages in trial runs and 99.8% product purity."
Why Cronus Raymond Mills Dominate the Market
Cronus’ dominance in calcium hydroxide and other mineral sectors stems from four pillars of excellence:
1. Precision Engineering
Every mill undergoes 72 hours of load testing with materials matching the client’s ore composition. Advanced laser alignment ensures roller concentricity within 0.05 mm tolerance—critical for vibration reduction and bearing longevity.
2. Smart Operation
The Xinjiang system features Cronus’ MillBrain® IoT platform, which monitors vibration, temperature, and output in real time. Predictive maintenance algorithms slash unplanned downtime by 40%, while remote diagnostics allow engineers in Shanghai to troubleshoot issues within hours.
3. Sustainability Edge
By recovering waste heat from grinding and recycling 95% of process air, Cronus mills cut CO₂ emissions by 1.2 tons daily compared to older models. This aligns with Xinjiang’s push for greener industrial practices amid its renewable energy boom.
4. Lifetime Partnership
Clients receive more than machinery; Cronus offers lifecycle support, including spare parts forecasting, operator training, and process optimization audits. "We don’t just sell a mill—we upgrade your entire production chain," emphasized CEO Wang Jun during the installation ceremony.
Expanding Horizons in Xinjiang and Beyond
Xinjiang, rich in limestone reserves and a hub for cross-border trade, represents a strategic growth area. The region’s calcium hydroxide output is projected to reach 2.8 million tons by 2025, driven by infrastructure projects and environmental regulations. Cronus has pre-sold six additional mills to Xinjiang clients, with plans to establish a regional service center by Q3 2024.
Cronus aims to capture 35% of China’s specialty grinding market by 2026. Upcoming launches include a modular mill for small-scale mines and a hydrogen peroxide-compatible model for advanced chemical synthesis.
Conclusion
The Xinjiang installation epitomizes Cronus’ fusion of R&D rigor and customer-centric engineering. By transforming calcium hydroxide processing from a bottleneck into a competitive asset, Cronus reaffirms its position as the partner of choice for industries demanding precision, reliability, and sustainability. As the global shift toward specialized mineral applications accelerates, Cronus stands ready to grind new paths to success.