In the field of industrial grinding, the 3-roller Raymond mill holds an important position with its unique advantages. It is widely used in multiple industries such as ore processing, chemical raw material treatment, and building material production, and is a key device for achieving fine grinding of materials.
I. Structure and Working Principle
1. Structural Design
The 3-roller Raymond mill is mainly composed of parts such as the main machine, analyzer, fan, finished product cyclone separator, pipeline device, and motor. The main machine part contains core components such as grinding rollers, grinding disc, and scraper. Three grinding rollers are evenly distributed at 120-degree intervals above the grinding disc. This layout makes the grinding force more balanced. The grinding disc rotates at a high speed driven by the motor, providing power for the grinding process. The scraper is installed on the edge of the grinding disc and is responsible for shoveling the materials and sending them into the grinding area between the grinding rollers and the grinding disc.
2. Working Principle
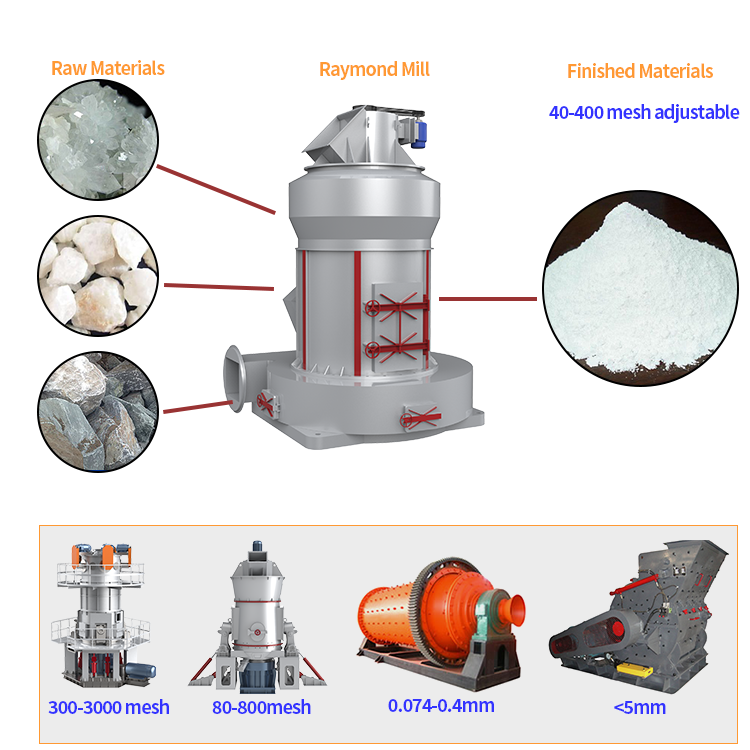
Materials enter the interior of the main machine through the feed inlet and land on the rotating grinding disc. Under the action of centrifugal force, the materials are thrown towards the edge of the grinding disc. At this time, the scraper shovels the materials and makes them enter the area between the grinding rollers and the grinding disc. The grinding rollers revolve around the central axis of the grinding disc on one hand and rotate on their own due to the frictional force between them and the grinding disc on the other hand. Under the combined action of revolution and rotation, the grinding rollers roll and grind the materials, gradually crushing them. The crushed materials are conveyed to the analyzer by the airflow generated by the fan. The analyzer generates centrifugal force through the high-speed rotating impeller to classify the materials. The fine powders that meet the particle size requirements pass through the gaps between the blades of the analyzer and enter the finished product cyclone separator, where they are collected as finished products; the coarse powders that do not meet the requirements are thrown towards the cylinder wall under the action of centrifugal force, then fall along the cylinder wall and return to the grinding disc for re-grinding.
II. Performance Advantages
1. High-Efficiency Grinding
Compared with some traditional grinding equipment, the 3-roller Raymond mill has a higher grinding efficiency. The three grinding rollers work simultaneously, increasing the grinding area and enabling more materials to be processed per unit time. Moreover, the materials of its grinding rollers and grinding disc are specially treated, with high hardness and wear resistance. While ensuring the grinding effect, it extends the service life of the equipment and reduces the number of equipment maintenance times, thus improving the overall production efficiency.
2. Fine Classification
The precise classification ability of the analyzer is a major highlight of the 3-roller Raymond mill. By adjusting the rotation speed of the analyzer impeller, the particle size of the finished product can be accurately controlled. Generally, it can produce powders with a particle size range between 80 mesh and 325 mesh, meeting the strict requirements of different industries for the fineness of materials. In industries such as chemicals and coatings, the fineness requirements for raw material powders are extremely high. The 3-roller Raymond mill can stably produce fine powders that meet the standards, providing a guarantee for product quality.
3. Energy Saving and Consumption Reduction
In terms of energy consumption, the 3-roller Raymond mill performs outstandingly. Its advanced structural design and reasonable power configuration result in low energy consumption during the operation of the equipment. For example, the optimized fan and pipeline system reduce the air flow resistance and the energy consumption of the fan; at the same time, the efficient grinding mechanism enables the materials to be ground in a relatively short time, avoiding energy waste caused by long-term operation and helping enterprises reduce production costs.
III. Application Fields
1. Ore Processing Industry
In the processing of metal ores, such as gold ore, copper ore, iron ore, etc., the 3-roller Raymond mill can grind the mined raw ores into appropriate particle sizes for subsequent ore dressing and smelting. For non-metal ores, such as calcite, dolomite, talc, etc., the ground ore powders are widely used in industries such as plastics, rubber, and coatings. For example, after being ground by the 3-roller Raymond mill, calcite is made into calcium carbonate powder, which is a commonly used filler in the plastics industry and can improve the hardness and stability of plastic products.
2. Chemical Industry
Many raw materials in chemical production need fine grinding. The 3-roller Raymond mill can efficiently grind various chemical raw materials, such as pigments, additives, catalysts, etc. When producing plastic particles, grinding the additives into uniform fine powders helps the additives to disperse evenly in the plastic, improving the performance of plastic products. In the rubber industry, fine grinding of rubber fillers can enhance the strength and wear resistance of rubber products.
3. Building Material Industry
In the production of building materials, the 3-roller Raymond mill plays an important role. It can be used to produce basic building materials such as cement, lime, and gypsum. By grinding raw materials such as limestone and clay into appropriate particle sizes, it promotes the chemical reactions during the firing process and produces cement products with higher strength and better quality. In addition, when producing building materials such as dry powder mortar and putty powder, the fine powders produced by the 3-roller Raymond mill can ensure the uniformity and construction performance of the products.
IV. Maintenance and Care Key Points
1. Regular Inspection
Regularly conducting a comprehensive inspection of the 3-roller Raymond mill is of utmost importance. The inspection contents include the wear conditions of the grinding rollers and grinding disc, the lubrication status of the transmission device, and whether the electrical system is normal, etc. For the grinding rollers and grinding disc, if severe wear is found, they should be replaced in a timely manner to avoid affecting the grinding effect and the operational stability of the equipment. Insufficient lubrication of the transmission device will lead to increased wear of components and an increased risk of equipment failure, so lubricating oil should be added regularly. At the same time, check whether the wiring connections of the electrical system are loose and whether the electrical components are damaged to ensure the safe operation of the equipment.
2. Replacement of Vulnerable Parts
During the operation of the equipment, some vulnerable parts such as scrapers, grinding roller linings, analyzer blades, etc. will gradually wear out. When these vulnerable parts are worn to a certain extent, they need to be replaced in a timely manner. Timely replacement of the scraper can restore the normal working state of the equipment.
3. Cleaning and Maintenance
Keeping the equipment clean helps to extend its service life. Regularly clean the accumulated powder and debris inside the equipment to prevent excessive accumulated powder from affecting the air flow transportation and classification effect. At the same time, clean the exterior of the equipment to avoid dust and debris from entering the equipment interior. In addition, regularly maintain key components such as the fan and motor, check whether the fan impeller is deformed and whether the motor heat dissipation is good, etc., to ensure the normal operation of all components of the equipment.
With its unique structure, high efficiency performance, and wide application fields, the 3-roller Raymond mill has become an indispensable equipment in the field of industrial grinding. Through reasonable maintenance and care, it can continuously and stably provide high-quality grinding services for the production of various industries and promote the development of related industries.