Jiangxi province calcium powder enterprise has mine reserves of more than 11.3 million tons and has 30 years of mining rights. The mineral powder factory covers an area of more than 30,000 square meters, and the factory building area is more than 10,000 square meters. It has 6 large-scale production lines, including 1 ore washing and crushing production line with a daily output of 1,500 tons; 3 80-600 mesh primary powder processing production lines, with an annual output of 150,000 tons; 2 600-mesh to 1,250-mesh fine powder processing production lines strips, with an annual output of 50,000 tons.
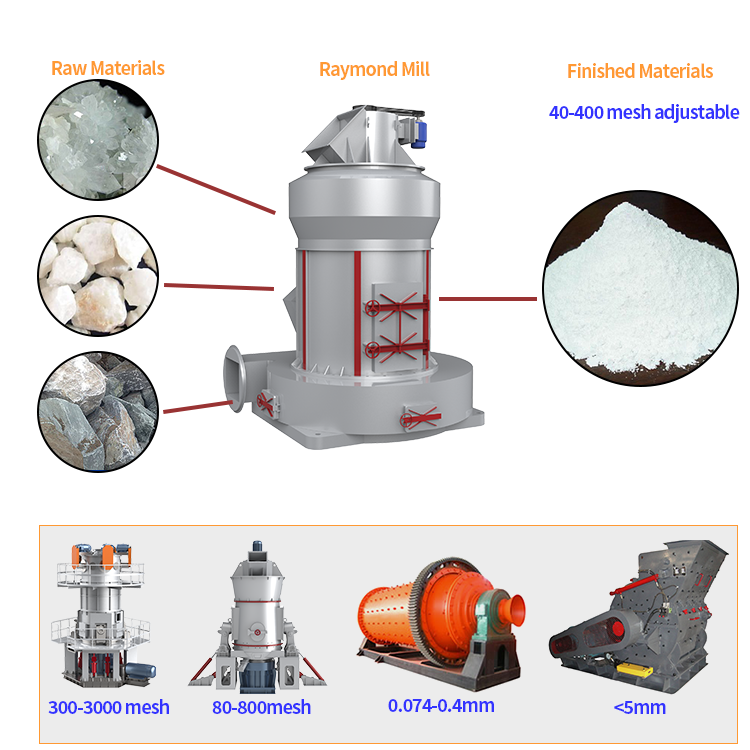
After being transferred and cooled, the raw materials are directly (or crushed once) continuously and evenly fed to the grinding chambers of 6 main machines through the feeder for grinding. The ground fine powder is classified by the classifier under the action of the fan airflow and then fed to the outlet. The air duct enters the collection stage, and the ground dust gas enters the cyclone collector through the air outlet duct of the main machine, and most of the finished fine powder is separated under the action of centrifugal force; at the same time, the excess gas is sent to the pulse dust collector and passes through the pulse dust collector. It turns into clean gas and is discharged, and the finished product fine powder collected by the bag is transported to the finished product conveying stage through the screw conveyor.
The finished mineral powder collected by the dust collector and cyclone collector is fed to the bucket elevator by the screw conveyor, and then enters the finished product tank. The dust gas in the tank is collected by the dust collector on the top of the tank and then the finished product is stored in the finished product tank, and the clean gas is discharged.